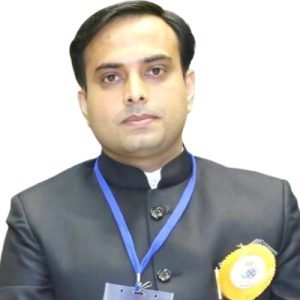
Satish Pandey Principal Scientist, CSIR-Central Road Research Institute and Associate Professor, Academy of Scientific and Industrial Research (AcSIR)
India is having world’s second largest road network in terms of length. Every year for maintenance and construction of this vast road network around 1.2 billion tonnes of natural aggregates are required. This huge demand of natural aggregates is meted out through unsustainable quarrying and mining of stone aggregates in many areas, which is causing serious ecological impacts on natural topography, flora and fauna. One of the best options will be to use Steel slag Valorisation as road making aggregates, writes Satish Pandey Principal Scientist, CSIR-Central Road Research Institute and Associate Professor, Academy of Scientific and Industrial Research (AcSIR)
During steel making, carbon rich molten pig iron is converted into steel in steel furnace and all the unwanted impurities are removed through various fluxing agents in the form of steel slag to maximize the iron content in the alloy. According to Indian Mineral Book 2018, steel slag output is approximately 20-30 % by mass of the crude steel production in the country which yields around 19.5 million tons of solid steel slag production annually in India. Majority of steel slag after metal recovery ends as waste dump or as land fill material. Such huge volume of steel slag cannot be landfilled for environmental and economic reasons. The utilization degree of steel slag varies from 0 to 50 % percent, on plant-to-plant basis depending upon course of action taken by steel plants for its disposal and utilization.
Steel slag Valorisation as road making aggregates can provide an attractive alternate to steel industries for its safe, productive utilization in road construction. CSIR-CRRI under the major research project sponsored by Ministry of Steel along with Arcellor Mittal Nippon Steel India has developed the steel slag valorisation technology for conversion of steel slag as road making aggregates. Processed steel slag aggregates developed through steel slag valorisation at AMNS India steel plant at Hazira have been successfully utilized in the construction of one km long six lane bituminous steel slag road connecting NH-6 to Hazira port at Surat, Gujarat.
Types of Steel Slag:

1. Lime pocket in LD steel slag
Steel making slag can be broadly classified in two categories based on steelmaking processes. The first is the Basic-Oxygen-Furnace (BOF) steelmaking process through which hot metal received from blast furnace is converted to steel. The second is the Electric-Arc Furnace (EAF) steelmaking process, which recycles mainly steel scraps. The steel from BOF and EAF can be further processed through a ladle refining unit i.e in an Ladle furnace to produce high-grade steels which is commonly referred as secondary steel making process. Each of these processes generates different types of slags.
Challenges with Steel Slag Utilization as Road Making Aggregates:

2. Heave in bituminous mix due to volumetric
Volumetric Expansion: Steel slag contains hydratable oxides (CaO and/or MgO) that can result in volumetric instability (expansion). Steel slag which is generated as an impurity due to the charge of fluxing agent in the furnace, shows volumetric instability due to the presence of free lime and free magnesia. A steelmaking slag may contain appreciable amounts of free lime (f-CaO) and small amounts of free magnesia or periclase (f- MgO), which causes expansive self-destruction by about 100% volume increase due to their reactions with water. BOF slag shows substantial high volumetric expansion in-comparison to EAF slag owing to presence of high CaO concentration. Untreated steel slag due to high volumetric expansion can cause detrimental effects on pavement durability and may lead to longitudinal and lateral cracks with heaves in bituminous, cement concrete and granular layers. Picture1 shows the free lime pocket in the untreated LD slag while the second shows the heave in bituminous mix due to volumetric expansion in LD slag aggregates.
Lime pocket in LD steel slag Heave in bituminous mix due to volumetric
Vesicular Texture and Porous Structure:
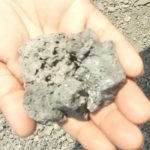
3. Irregular and Vesicular texture
In comparison to natural aggregates, the microscopic surface of steel slag has pitted and vesicular texture and porous structure. The cellular or vesicular texture results from the bubbles of the gases which have been dissolved in the liquid slag. Vesicular texture and porous structure may lead to higher water absorption which in turn lead to higher bitumen, cement consumption in comparison to natural aggregates. Picture 3 shows the irregular vesicular texture at macroscopic level while picture 4 shows the porous structure at microscopic level.

5. High pH leachate from slag dump
High pH and Heavy Metal Leachates: Steel slags may contain heavy metals such as antimony, arsenic, barium, beryllium, cadmium, chromium, cobalt, copper, lead, mercury, nickel, selenium, thallium, vanadium, etc. Even though these metals are available as minor constituents of steel slag, possible leaching of these heavy metals into groundwater and native soil should be prevented. BOF steel slag owing to presence of high CaO can emanates high pH leachates which can make the near by water and soil body alkaline in nature. These alkaline leachates can increase water pH and results into a increased chemical oxygen demand (COD) besides increasing salinity. Pictures 5 and 6 show the possible leachate contamination from unprocessed steel slag dumps in near by soil and water bodies. Probability of leaching from the slag can be considerably reduced by developing stable mineralogical phases in the slag and subjecting it on appropriate processing mechanism by adopting suitable steel slag Valorisation technology based on steel slag types.
Valorization of Steel Slag as Steel Slag Aggregates :
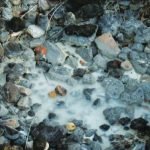
6. High pH leachate in water bodies
A sustainable circular economy wants reduce dependency of society on natural resources by ensuring the utilization of available resources again and again, up to best possible extent.
Processed steel slag aggregates due to its improved physical and mechanical properties can be utilized in all layers of steel slag road as substitute of natural aggregates. A customized steel slag Valorisation technique comprising customized steel slag cooling procedure, followed by appropriate slag treatment and metal recovery process based on type of steel slag and chemical composition can produce sound durable steel slag aggregates for road making. Picture 7 shows the processed steel slag aggregates generated through customized steel slag Valorisation technique developed by CRRI for conversion of steel slag as road making aggregates.
Steel Slag Road:

7. Aerial view of steel slag road
Conventionally bituminous roads are constructed using natural aggregates and bitumen. Natural aggregates occupy 95 to 96 % volume of the road while bitumen is utilized as binder along with natural aggregates in surface layer of the road and occupy 4 to 5 % volumetric space in surface layer. Steel Slag Road at Hazira, Surat, Gujarat is constructed using Processed Electric Arc Furnace steel slag aggregates by substituting natural aggregates in all layers of bituminous road. Around one lakh tonne EAF steel slag aggregates were utilized for the construction of one km. long six lane bituminous steel slag road connecting NH-6 to Hazira port at Surat Gujarat. All layers of steel slag road such as subgrade, sub-base, base and wearing course along with road shoulders and median were built using processed steel slag aggregates.
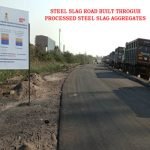
8. Longitudinal view of steel slag road Pic Courtesy: Arcelor-Mittal Nippon Steel India Ltd
This heavy duty steel slag road is designed for 100 MSA (Million Standard Axle Repetition) design traffic for 20-year design life period and subjected on heavy commercial traffic i.e 1000 to 1200 commercial vehicles per day carrying 30 to 40 ton pay load for past two years. Owing to novel design composition and improved stiffness of pavement layers “Steel Slag Road” is built with 32 % less thickness in comparison to conventional bituminous roads as recommended in Indian Road Congress standards and guidelines.
Pictures 8 and 9 show the aerial and longitudinal views of steel slag road at Hazira Surat. Periodic performance evaluation carried out by CSIR- CRRI shows that the structural stiffness of steel slag road despite the reduced thickness is 40 to 50 % higher than the conventional bituminous road.
Key benefits of steel slag road:
Environmental
- Eco-friendly sustainable utilization of steel slag waste
- Saving of road making Natural Aggregates
- Reduction of GHG emissions in road construction
- Reduction in carbon footprint of road construction
- Prevention of potential land, air and water pollution due to unscientific disposal of steel slag as solid waste
Technical
- Improved durability of road with better service life
- Higher load resistance capacity
- Reduced Road Thickness
- Improved skid resistance
- Economical than conventional bituminous road in nearby areas of steel plants
The first steel slag road built by CSIR-CRRI and AMNS India has received many national and international acclaims for its technological features.